Amidst rising operating costs and a shortage of skilled workers, mining companies are constantly looking for ways to increase overall efficiency, save costs and retain talent, while mitigating the safety hazards present in underground mines.
The importance of efficient ventilation
Beyond compliance with regional safety standards and regulations, investing in a reliable, high-efficiency ventilation system can also help mining organisations remain competitive and profitable by optimising energy consumption and ensuring employee health, safety and productivity – ultimately saving costs. In addition, providing a safe and stable working environment for employees can help mining companies retain their existing workforce and attract new talent in a limited candidate market, which can further enhance productivity and reduce talent acquisition costs. However, it is critical to invest in ventilation equipment suited to the real world rigours of a mine’s environmental conditions to reduce unforeseen energy and maintenance costs. While working with an experienced engineer is recommended to ensure proper fan selection for mining applications, the following provides an overview of key factors to consider when selecting a ventilation system for both safety and efficiency.
Common safety hazards
Ventilation system designers first need to ensure that equipment addresses all of the health and safety hazards of the application. Common hazards in underground mines include inadequate or diluted oxygen levels; dust and particulates in the air; noxious and flammable gases; and unsafe temperature and humidity levels. Even before these hazards reach dangerous levels, poor working conditions can hamper productivity and lower worker morale.
Oxygen deprivation
The first safety hazard to address is the risk of oxygen deprivation. Ventilation solutions must ensure that workers have a continuous supply of oxygen at the required levels. This also means keeping other gases in check. Even non-toxic gases such as nitrogen, carbon dioxide and hydrogen can displace oxygen in the air and lead to asphyxiation.
Particulates in the air
Dust, particulates and byproducts from underground tunnels and passageways must be diluted or removed from the air. Both inspirable dust (large particles) and respirable dust (microscopic particles) pose a risk to worker safety and should be reduced or eliminated from the working environment. For example, diesel particulate matter is a common particulate in mines and is formed by machinery that uses diesel fuel. Without appropriate ventilation, exposure to diesel exhausts – which includes both gas and particulate – causes health concerns for workers.
Flammable and toxic gases
Toxic and potentially flammable gases are another common concern in mines. In high enough concentrations, combustible gases like methane can lead to risk of explosion. High concentration areas can occur naturally when gases are released from layers of rock that are being excavated. A secondary concern from methane combustion is the production of carbon monoxide (CO), an extremely toxic gas. Exposure to CO, even in small amounts, can lead to long-term health problems or death.
Unsafe temperature and humidity levels
Very high or very low temperatures and high humidity levels can also pose a risk to employee health and reduce productivity. Humidity levels are impacted by a variety of factors, including how much water is used for dust suppression, the types of drilling equipment used and the higher than average moisture levels already present in mines.
Selection of primary fans
Choosing the proper primary fans for a mine ventilation system is fundamental to reducing the safety hazards in mining applications. However, it is also important to choose the right equipment to ensure energy efficiency and to consider initial costs alongside long-term operating and maintenance costs.
One of the main challenges when selecting fans for these applications is that real world constraints can seriously impact the performance and efficiency of the fan, so specifications derived from ideal laboratory conditions are deceptive and can make it difficult to accurately choose ventilation fans for performance and efficiency. The key is to take into consideration the real world system effects on fan performance, power and energy usage as accurately as possible early in the selection process. The most important factors to consider include air flow requirements, pressure requirements and the unique constraints of the location and environment.
Note that there are several types of fans used in mining applications. Primary fans are used at both the intake side to push air into the tunnel or shaft entryway and at the return side to pull air out of the tunnel system. In addition, auxiliary or booster fans are used to create additional air flow. This article focuses on primary ventilation fans (axial and centrifugal) because the ability to control fan type, arrangement and duct design to minimise system effects is more easily achieved on the large primary vent fans.
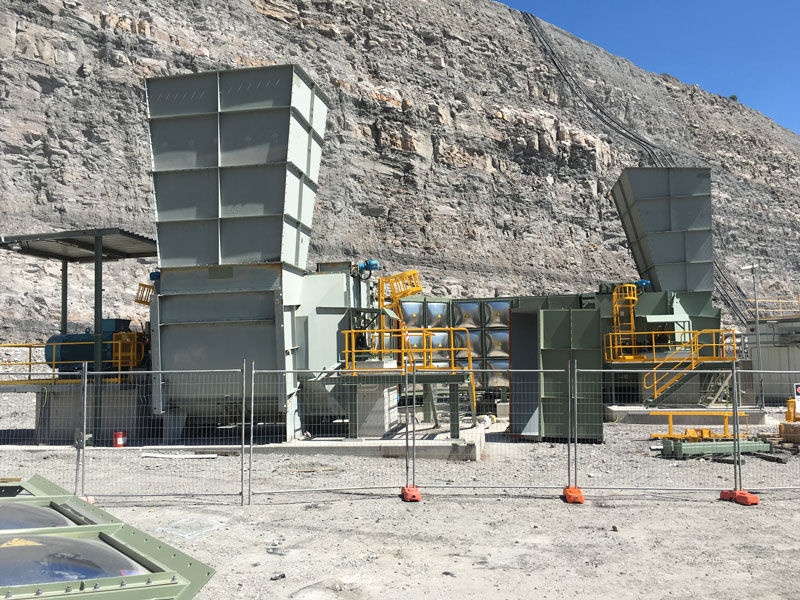
Accounting for real world conditions
Real world conditions in the mining industry can vary widely from standard laboratory conditions and these differences affect fan performance and efficiency. In the real world, shaft covers, dampers, ducts expanding and contracting, heaters, coolers, demisters, silencers, diffusers and more must be accounted for. Each one of these introduces system effects that impact each piece both downstream and upstream of the fan and change the flow of air into and out of the fan.
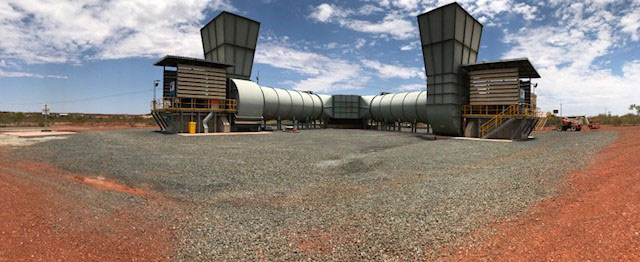
For example, one of the most important factors in mining ventilation is directing air to areas that are being used, while reducing or limiting air flow in vacated areas. This can help increase efficiency and decrease operating costs. Flow can be manipulated using regulators and walls to reduce air flow into specific areas. In addition, flow rate can then be monitored to ensure proper ventilation, find and correct leaks and verify the operating point of all fans in the system.
When fans are tested in laboratory conditions, inlet or outlet ducts can be ideally situated to achieve laminar flow and then measurements are taken in the laminar flow. However, in real life applications, the flow into the fan is not perfect. There is non-laminar flow with rotation and uneven profiles which can degrade the fan performance and change the efficiency. It can also change the size and position of the best efficiency regions within the performance curve from what was recorded in the original laboratory test.
Understanding the air flow requirements of the application upfront, as well as the impact of real-world constraints on air flow, will help with the selection of the appropriate fan for the application.
To account for the demands of the application, it is important to document several important pieces of information at the beginning of the project, including:
- Aerodynamic and noise requirements
- A sketch showing dimensions of connections to the fan system and where pressure is needed
- Corrosive and erosive properties of the air
- Power type available (voltage, frequency)
- Environmental conditions
- Site location and physical limitations
- Required equipment life and reliability
With this information, a system designer can begin the iterative process of picking the fan, calculating the system losses and flow conditions, and mechanically designing the fan. This process is repeated to identify the convergence of the ‘best’ fan for performance, quality, cost and reliability.
Accurate calculations are key
In the industry, it is common to calculate system losses incorrectly and be off by 10 – 50% in the pressure and flow requirements needed from the fan. In addition, many do not take the time to calculate the actual system resistance curve to see where it is falling against the laboratory-generated fan curve, nor do they complete an in-situ fan test to determine the decrease in fan efficiency from the non-laminar flow entering the fan. The costs of inaccurately accounting for these losses add up quickly.
For example, consider a 1500 kW primary mine fan at 3.0 kPa and 300 m3/s. If the fan experiences 10% higher pressure from system effects, the system resistance curve is now at 75% efficiency instead of 82% efficiency. Therefore, the power increase would be 200 kW.
System effect operating cost = 200 kW × 24 hr × 365 d × 10 yr × US$0.15/kWh = US$2 628 000.
In this example, the impact of incorrectly calculating pressure through the fan by 10% multiplies to US$2.6 million in additional operating costs over 10 years of continuous operation.
Case study
Calculating these factors correctly up front will help ensure long-term success. In one recent case study, a gold mining company reduced operating costs and improved safety by installing a high efficiency mine ventilation solution. In this application, one of the biggest challenges was safeguarding workers deep in the mine and funnelling cool air from the surface to the workers below. Temperatures at the bottom of the mine would climb to approximately 30°C, creating a punishing environment for the miners below the surface.
As part of a major mine improvement project, the mining company worked with a trusted vendor partner to specify a ventilation system solution, including primary fans, the electric power unit and civil construction system. Installing this system not only improved the safety and comfort of the miners, but it also provided a static efficiency in excess of 85%, which helped the mining company save on long-term energy costs.
Conclusion
When designing a high efficiency ventilation system for mining applications, it is important to carefully consider all possible health and safety hazards early in the selection process, as well as unique challenges and constraints of the location and environment. For many mining applications, a custom engineered solution is needed to meet the precise application requirements and will keep the operation running efficiently, improve productivity and profitability and preserve the health and safety of the workforce. Partnering with a knowledgeable and experienced ventilation equipment manufacturer can help in customising the right solution for the application.